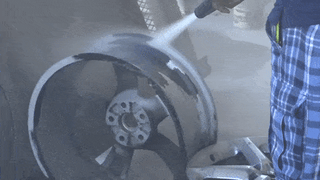
Powder coating is well known for its adhesion and durability, and is commonly used for automotive parts, construction equipment, offshore platforms, and more.
However, the qualities that make powder coating such a great coating can become big challenges when you need to remove it.
The most common methods to remove powder coating are:
- Chemical stripping
- Burn-off in oven
- Media blasting
1. Chemical Stripping
Chemical stripping methods can go by several names. You might hear them referred to as "caustic" or "solvents." They work by causing the powder coating to dissolve, soften, and/or swell. At this point, the coating will fall off or have to be washed off.
Chemical stripping can remove powder coating completely and evenly. It is also inexpensive and available at most hardware stores, so it's well suited for the small or occasional project.
Considered dangerous and hazardous
Chemical stripping also has disadvantages. The toxic chemicals are dangerous to work with, as they can easily burn the operator's skin and eyes. Proper PPE (personal protective equipment) is required.
Disposal is also troublesome because both the used stripper and the water used to rinse the part are considered a hazardous waste and must be disposed of accordingly. The disposal process can be a costly headache, with lots of money and paperwork involved.
Does not inherently leave an anchor profile
One final thing to consider is the desired anchor profile of the surface being stripped. An anchor profile refers to the microscopic texture of the surface, which gives the new paint or coating something to adhere to. This is critical for the longevity of the new coating — learn more about anchor profiles here.
Chemical strippers leave behind a perfectly smooth surface, so you may need to scuff up the surface before applying a new coating. This adds an extra step to your process. One exception would be if the surface was given a proper anchor profile before the original coating was applied.
2. Burn-off in Oven
Thermal removal methods use very high temperatures to burn off powder coating, which turns to ash and must then be washed off. These methods may be referred to as "burn-off," "bake-off," or "fluidized bed."
Thermal stripping is quite popular because it's one of the quickest ways to remove powder coating. It doesn't come with the same environmental concerns of chemical stripping.
Requires lots of power
Not only is the required equipment expensive, but supplying the necessary power is even more costly. Think your heating bill is outrageous in the wintertime? Warming your house is nothing compared to these huge ovens, which maintain temperatures up to 1200°F! It can even be challenging to find a location where sufficient power is available.
Can warp and damage parts
The extremely high temperatures required to remove powder coating may warp or damage parts. Like chemical stripping, this method does not leave an anchor profile which is critical for the reapplication of paint or coating.
3. Media Blasting
Abrasive blasting, which includes both traditional sandblasting and Dustless Blasting®, uses media propelled at high speed towards the surface to strip off the powder coating. Dry blasting can take place in a blast cabinet or a blast room, whereas Dustless Blasting requires minimal or no containment.
Wet vs. dry blasting for powder coating
Traditional sandblasting can be a slow process for powder coating removal, and is not always favored. Because the Dustless Blasting process introduces water, it increases the mass and energy that the machine is putting out, making it dramatically faster than dry blasting. The water also cools the powder coat, making it brittle. This allows it to flake off as opposed to getting gooey, like it does with the heat generated from dry blasting.
The mobile advantage
Because Dustless Blasting uses water to suppress the dust plume, the process is environmentally friendly and does not require bulky containment. This makes it perfect for blasting items that can't fit into a blast cabinet, or can't be moved. You can even take our mobile units to the customer's location and blast safely just about anywhere.
Superior paint or coating reapplication
By using different abrasives, you can achieve various anchor profiles with media blasting. As mentioned previously, the correct anchor profile is critical for the reapplication of paint and coatings.
What about rust?
The water in the Dustless Blasting process is no problem for metal surfaces, due to our Rust Inhibitor. Simply rinse the metal with diluted rust inhibitor after blasting, and you will prevent flash rust for up to 72 hours. The surface is left clean and ready for the new coating.
In conclusion
There are many ways to remove powder coating. Although Dustless Blasting is our favorite method, you might find that another process is the most suitable for your project. To learn more about using Dustless Blasting to remove powder coating, check out these additional blog posts.