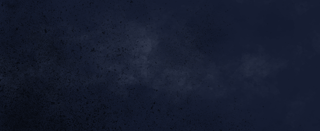
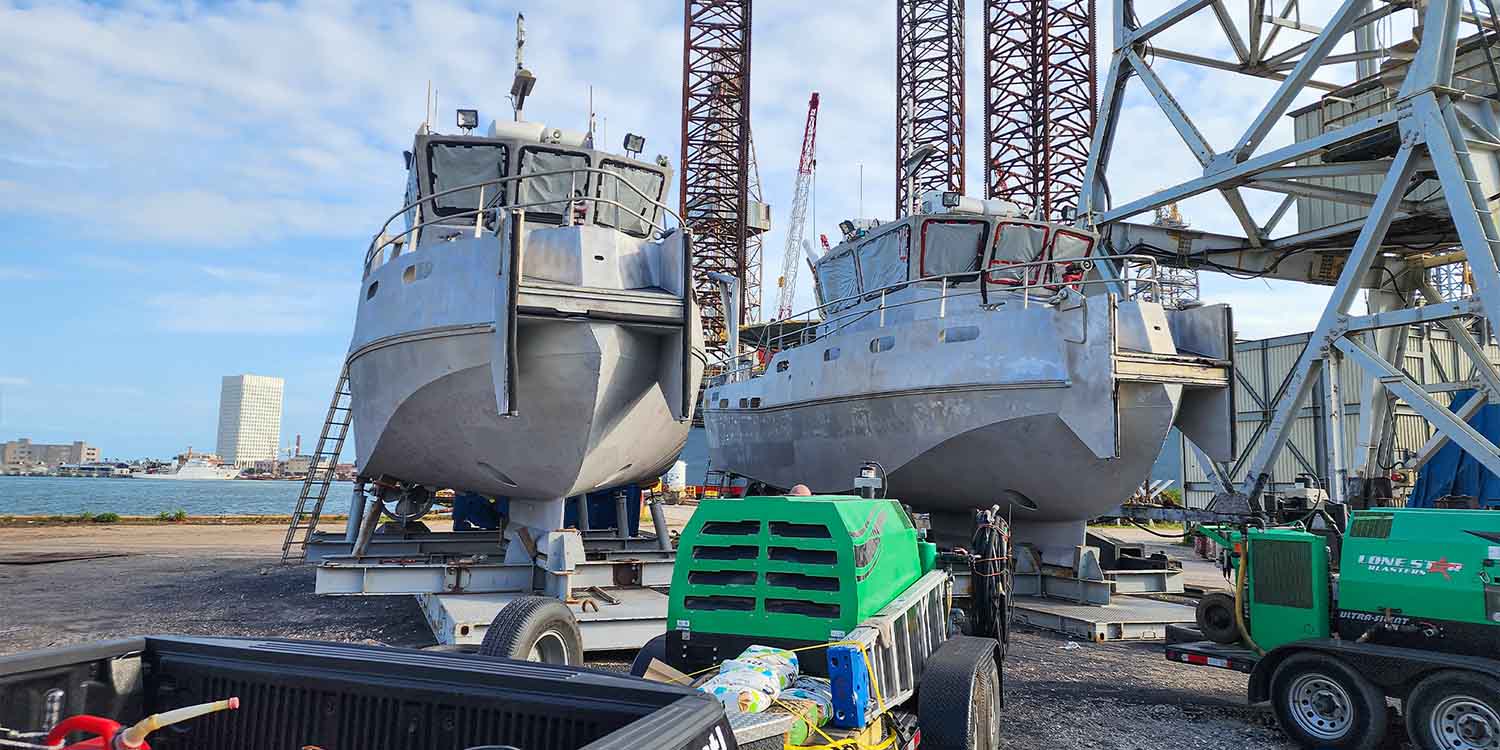
In an impressive feat of teamwork, two Texas-based blasting companies joined forces to rid two 40-foot metal boats of marine paint, anti-fouling, and bondo in less than a day.
We conducted a hands-on comparison of the popular SLV-5 and SLV-6 blast nozzles in order to demonstrate how nozzle size affects blasting performance.
The advantages of upsizing your blast pot are well known: The increased abrasive capacity of a larger pot allows for longer continuous blasting and fewer refills throughout the workday.
However, many aren't as familiar with the advantages of upsizing your blast nozzle, which can significantly boost your blasting productivity (provided your compressor can supply the required CFM).
To demonstrate, we set up two mobile blasting machines:
Two 4' x 4' squares were wet blasted - one using the SLV-5, and the other using the SLV-6.
After testing with wet crushed glass, the blast pots were emptied of remaining media and the test was repeated using wet pyroxene blast media.
The testing area was prepped, treated with 2-part epoxy paint, and then divided into 4' x 4' squares.
To run this demonstration, we utilized the renowned DB500 Mobile S and its SLV-5 blast nozzle, in addition to its high-performance limited edition variant that comes equipped with an SLV-6.
Aside from their blast nozzle, both machines utilized the same blast settings:
With the goal of determining the performance difference between the SLV-5 and SLV-6 nozzles, we recorded each machine blasting separate squares. The test was repeated twice, first using crushed glass, and finally using pyroxene media. In total, four separate 4' x 4' squares were blasted (totalling 64 sq ft of testing area).
During our demonstration, upgrading the nozzle size from #5 to #6 had a substantial impact on blasting productivity.
The SLV-6 nozzle outperformed the SLV-5, boasting a removal rate that was anywhere from 17% to 53% quicker.
Bear in mind, these impressive gains were realized with the media flow remaining constant across both units. This means the media consumption rate did not change. The secret behind this leap in productivity lies solely in the upsized SLV-6 nozzle, when measured against the SLV-5.
Interestingly, we also measured a significant abrasion speed increase when swapping from crushed glass to pyroxene media. Read more about pyroxene media and our findings in this related blog article.
Thinking about upgrading to a larger nozzle? Be aware of your air supply constraints.
To determine whether a larger blast nozzle would be more productive for you, determine what blast pressure (PSI) you need to maintain for productive blasting and what volume of air your available compressor can supply per minute (CFM), then consult this nozzle size chart to find the nozzle orifice size that meets those parameters. Reserve adequate capacity for additional tools that will also require your air supply, like an air dryer and cooler system and a blast respirator.
Learn more about picking the right nozzle for the job.
For example, if you own a classic DB500 Mobile S, while a nozzle size increase might seem like a good idea, you may find that your compressor just doesn't have enough CFM for all of your equipment and a NO.6 (3/8") nozzle. This is why the DB500 performance limited edition is so exciting. With an upgraded 250 CFM compressor, there's more than enough air capacity for the nozzle size increase to a NO.6.
With an upgraded compressor, the performance model of the DB500® Mobile S has ample power to accommodate a larger nozzle size than the standard DB500® Mobile S, from #5 to #6, resulting in a 44% total increase in total nozzle area.
This increased range of workable nozzle sizes offers the blaster increased versatility in their blasting setups. Whether your focus is on maximizing particle velocity or widening your blast pattern, this upgraded system is your solution for achieving both goals.
Fill out the form below and get a printable document of our findings with even more insights.
Investing in this versatile machinery will streamline operations and boost profitablility. No longer are you having to waste time and money on outdated methods or outsourcing.
Whether it's used to restore classic cars, boats, or antiques - the applications for dustless blasting are seemingly endless and can help existing businesses expand their offerings and generate increased income.
Dustless Blasting can strip away unwanted, tough coatings from surfaces. Our machines offer an advantage over traditional sandblasting – significantly less dust and more productivity per pound of abrasive.
In an impressive feat of teamwork, two Texas-based blasting companies joined forces to rid two 40-foot metal boats of marine paint, anti-fouling, and bondo in less than a day.
A swift solution was needed when blisters were discovered on the fiberglass gelcoat of this 54-foot vessel. And that's where Dustless Blasting stepped in as the clear choice.
Two blasting companies collaborated and leveraged DUSTLESS BLASTING® equipment for an industrial-scale water treatment plant project.