Industrial Surface Preparation Solutions for Manufacturing and Fabrication
Tackle Tough Jobs with Dustless Blasting® Equipment Designed for Cleaning Steel and Surface Prep
In manufacturing, production doesn’t pause for surface prep problems. Whether you're cleaning steel beams, prepping parts for coating, or removing rust from machinery, your equipment needs to be reliable, fast, and efficient. That’s where Dustless Blasting® comes in — providing innovative surface preparation solutions built to meet the heavy demands of the manufacturing industry.
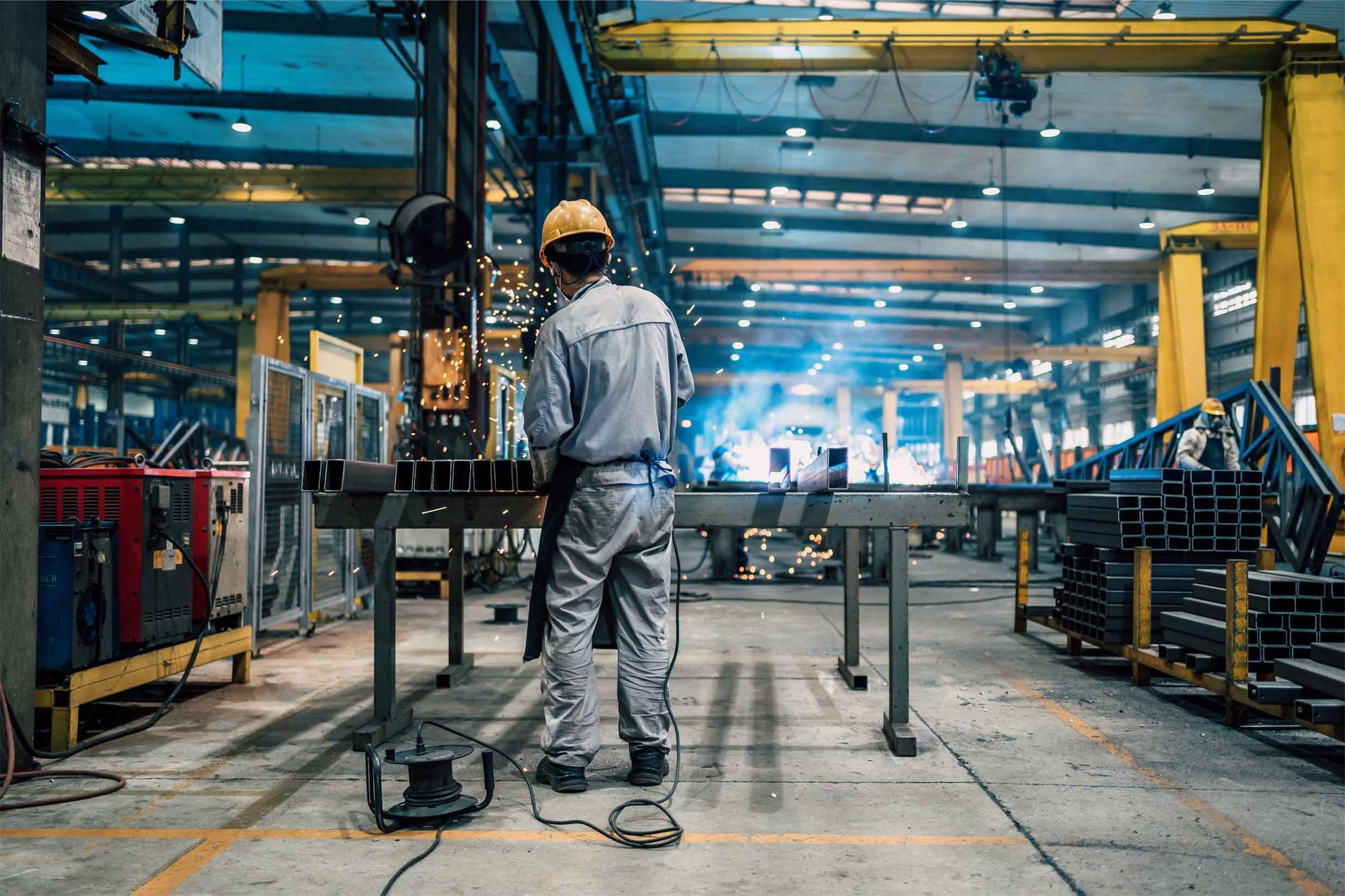
Surface Preparation Challenges in Manufacturing
Manufacturers face a unique set of challenges when it comes to industrial surface preparation:
-
Built-up coatings and rust on steel components can delay production or compromise quality.
-
High maintenance costs for heavy machinery—if corrosion sets in due to poor surface preparation or coating failure, expensive repairs or full refurbishments may be required.
-
Tight environmental regulations require dust suppression and responsible waste handling.
-
Operator and worker safety concerns—traditional dry blasting can create airborne contaminants and visibility hazards, increasing health risks and the likelihood of accidents.
-
Inefficient surface prep methods slow down turnaround time for parts and finished products.
-
Coating adhesion failures — without proper surface preparation, even the best industrial coatings will peel, flake, or fail prematurely, resulting in rework and increased costs. Failure to remove rust, grease, and other foreign matter can compromise surface quality and lead to poor adhesion.
When precision, cleanliness, and speed matter most, outdated or underperforming methods like grinding or dry sandblasting simply don’t cut it. Achieving a clean surface is essential for both coating and adhesive bonding applications, as contaminants can cause coating failures. Industry standards often require cleaning down to bare metal, especially when working with painted or previously coated surfaces, to ensure optimal adhesion and durability.
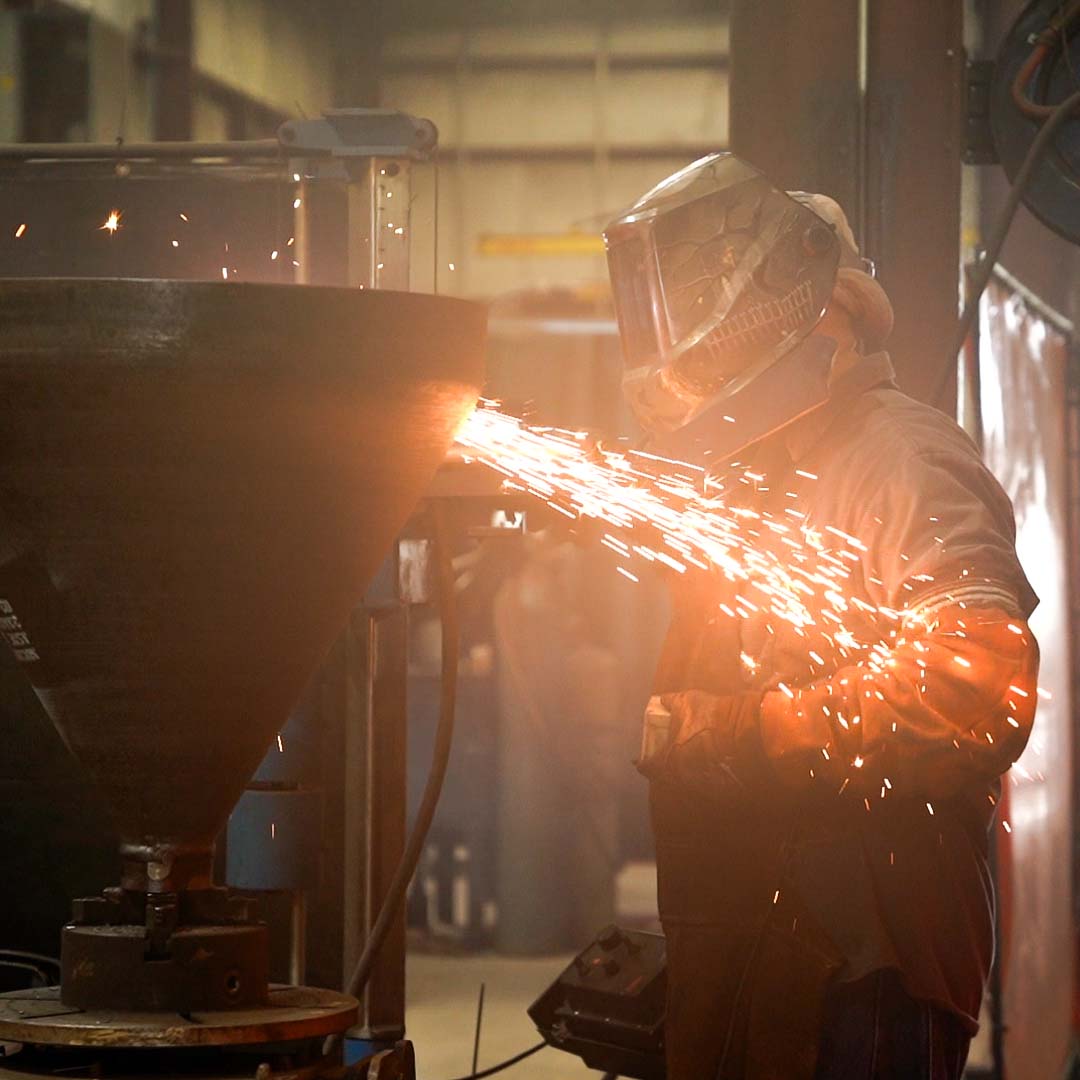
Removing Surface Contaminants
Eliminating surface contaminants is a fundamental aspect of effective surface preparation. Contaminants such as dust, dirt, grease, oil, and residues from existing coatings can interfere with the adhesion of new coatings or adhesives, leading to costly failures down the line. To achieve a truly prepared surface, manufacturers rely on a range of surface preparation methods tailored to the specific contaminants and materials involved.
Abrasive blasting is a powerful technique for stripping away old coatings, mill scale, and embedded contaminants, leaving the substrate clean and ready for further treatment. For less severe contamination, power tool cleaning and hand tool cleaning—using wire brushes or sanding discs—can efficiently remove loose debris and smooth the surface. Selecting the right method ensures that the surface is free from contaminants, providing a clean foundation for optimal coating or adhesive performance.
What Manufacturers Are Using Dustless Blasting For
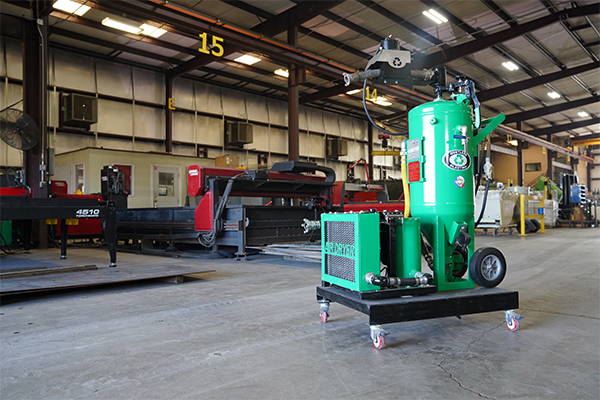
- Cleaning weldments, structural steel, and fabricated assemblies
-
Removing heavy coatings from equipment or tools
-
Surface prep before powder coating application or painting, ensuring the surface is free of old paint and properly prepared
-
Removing e coat and preparing bare metal for subsequent treatments, following standards that require a clean, contaminant-free surface for optimal adhesion and corrosion resistance
-
Rust and corrosion removal in routine maintenance
-
Refurbishing steel molds, fixtures, and conveyor systems
Dustless Blasting® for Proper Surface Preparation
Dustless Blasting® offers a better way to handle cleaning steel and prepping surfaces across a wide range of manufacturing applications. It is highly effective on a variety of metals, including carbon steel and galvanized steel, making it a versatile solution for different substrates.
The system efficiently cleans surfaces and removes oils, failing coatings, mills cale, residue, and stains, ensuring optimal preparation for subsequent processes. With Dustless Blasting®, you achieve a residue-free surface, ready for coating or painting.
- Gentle on Substrates: Remove rust, mill scale, coatings, and corrosion from steel structures, machinery, and parts without warping or damaging the base metal. The process is capable of cleaning down to bare metal surfaces, effectively removing iron oxide and other corrosion products for optimal results.
- Wet or Dry Blasting Options: Pair your equipment with an air dryer for dry blasting, or use our dust-suppressing wet method for cleaner, safer workspaces.
- Fast, Efficient, and Precise: Blast with more speed and less mess than traditional prep methods, helping you minimize downtime and maximize productivity.
- Surface-Ready Results: Our process leaves behind a clean, profiled surface ideal for coating or painting—reducing the risk of adhesion failures.
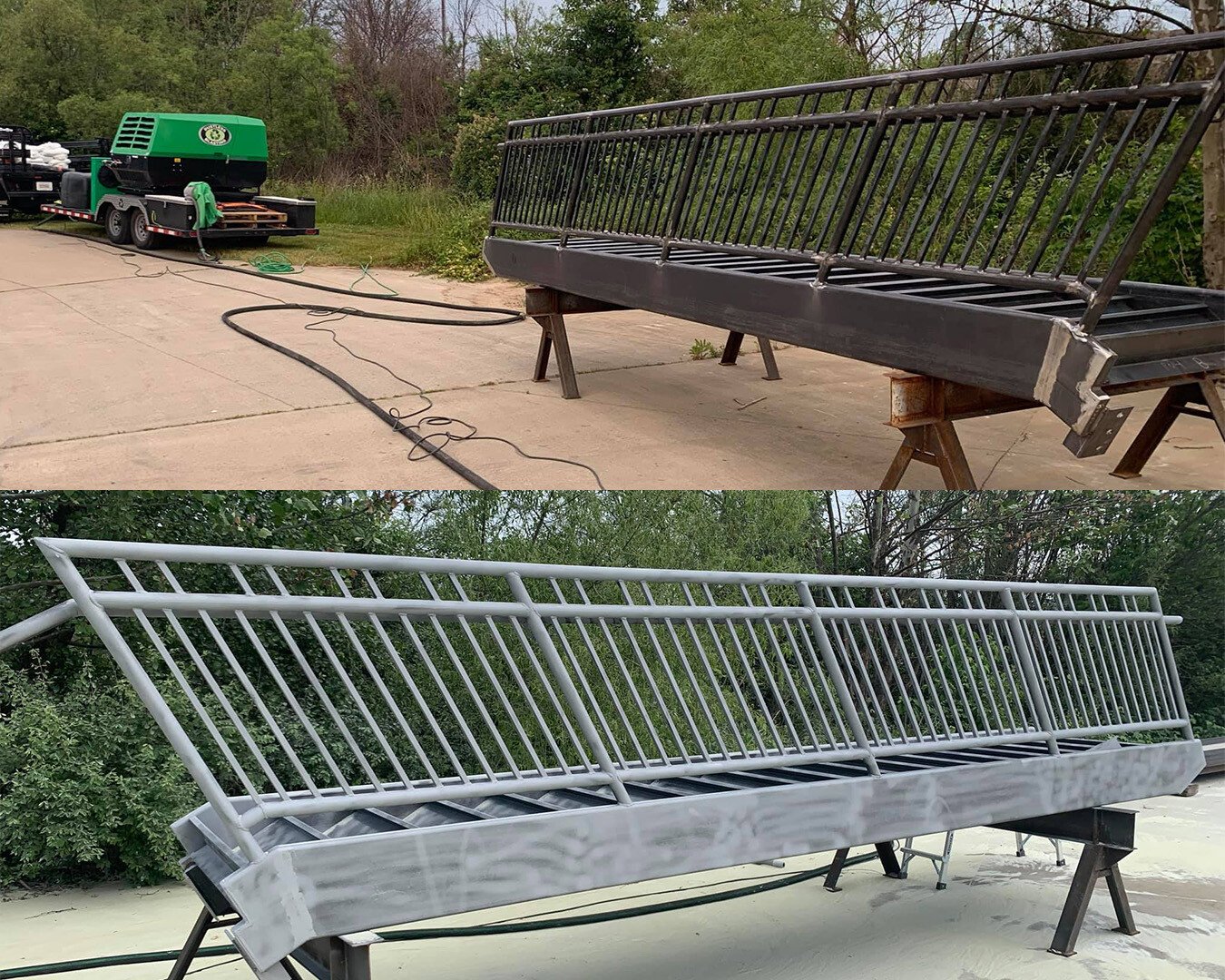
Mill scale removal with Dustless Blasting
Surface Preparation Solutions That Work
From compressor-ready carts to fully mobile blasting systems, we have a solution that fits your facility.
Dustless Blasting® systems are engineered to perform reliably even in environments with high temperatures, such as refineries, tanks, and turbines, ensuring durability and consistent performance. Compared to traditional cleaning tools, Dustless Blasting® offers superior effectiveness for tough industrial cleaning jobs and achieving fine finishes.
Compressor-Ready Carts
Perfect for businesses who already own a compatible air compressor. These systems feature:
-
Blast pot: ready for wet or dry blasting applications
-
Air dryer and cooler: critical for preventing clogs when dry blasting
-
Use any abrasive, including sodium bicarbonate for thin aluminum and delicate substrates
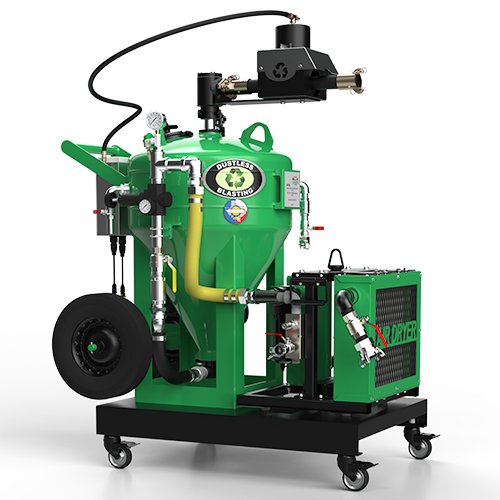
Blast Pots
Ideal for in-shop use—just hook up to an air source and start blasting.
These systems feature:
-
Adjustable pressure settings capable of removing just about any coating from any surface without damaging the substrate.
-
A variety of media choices: crushed glass, glass beads, garnet, coal slag, plastics, etc.
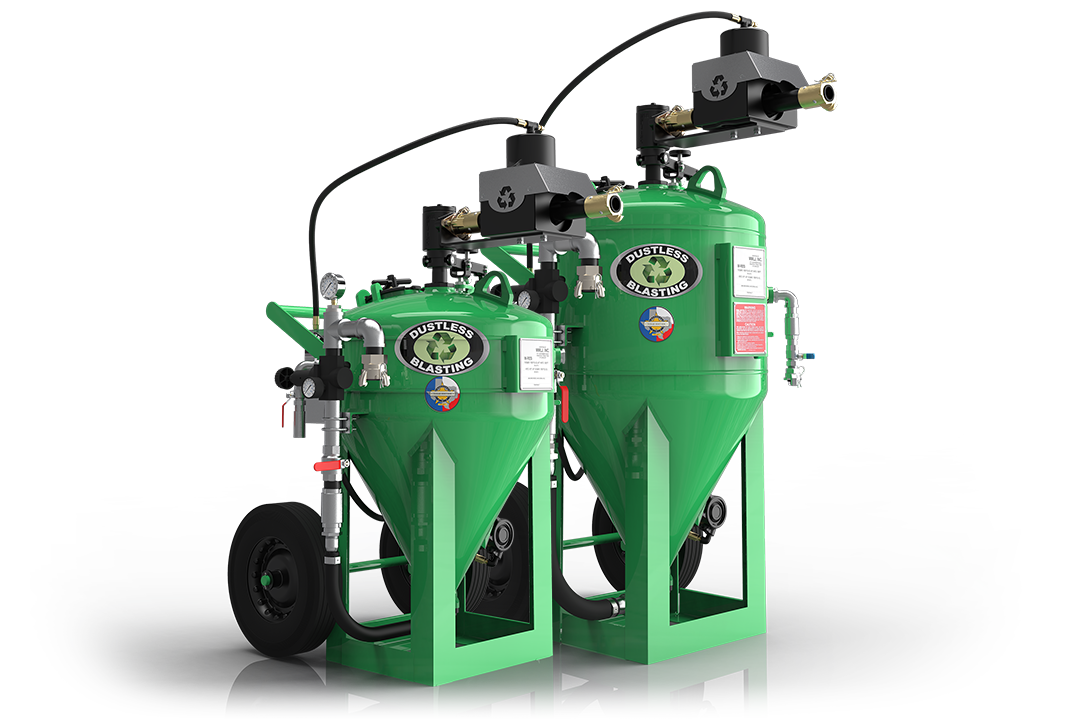
Blasting Trailers
For teams that need a fully self-contained with it's own air source. Every mobile unit includes:
-
Onboard air compressor
-
Blast pot for wet or dry blasting
-
Built-in air cooler and dryer, allowing for dry blasting and media use with zero moisture issues
-
Trailer-mounted, ready-to-go system, no setup required
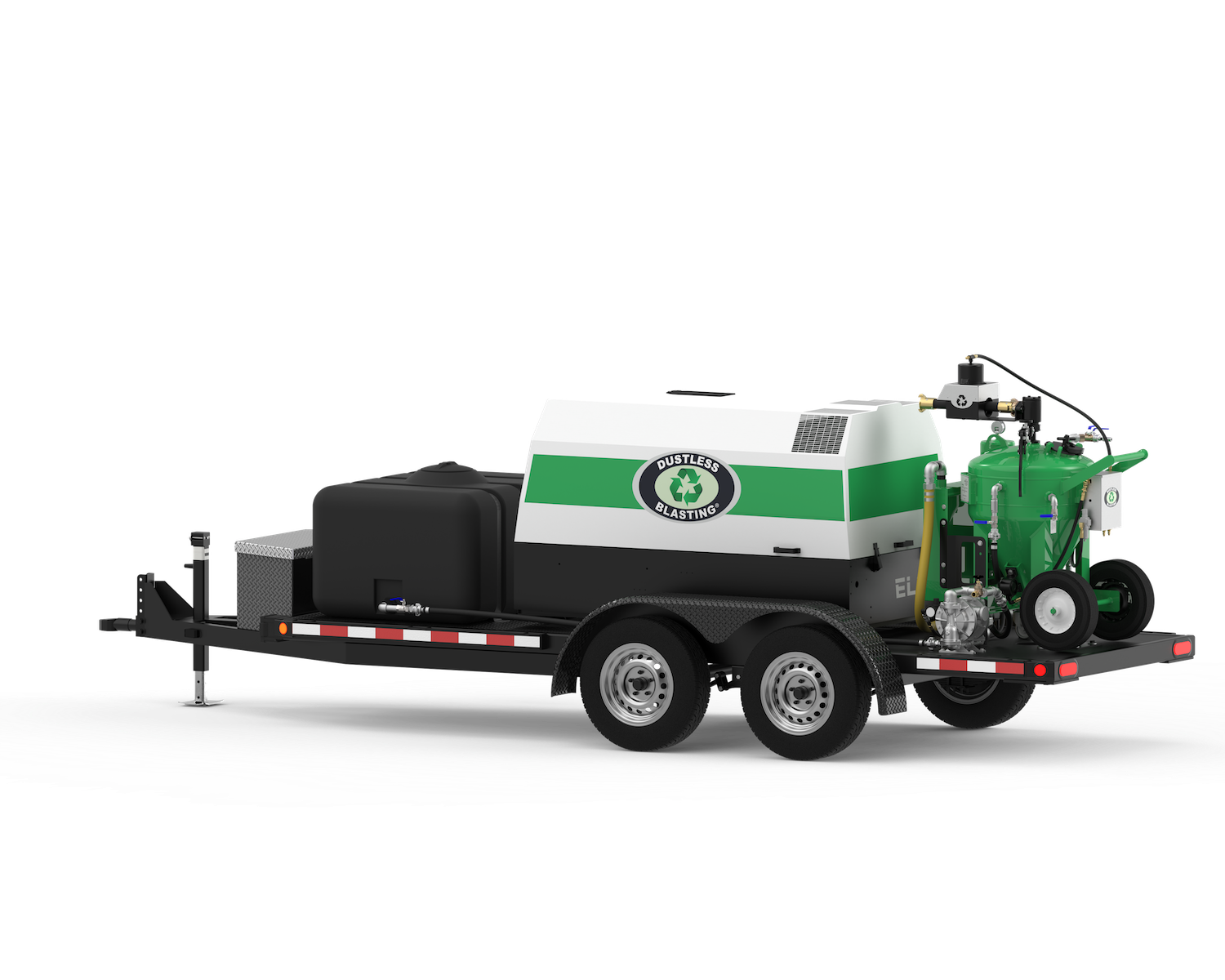