Powder Coating Process
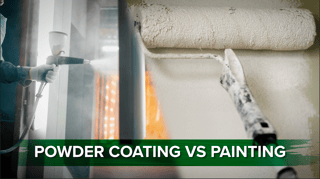
Powder coating is a durable finish that can offer an array of added protections for the substrate. Depending on the resin used, the powder coated materials may have additional corrosion resistance, chemical resistance, heat or UV light resistance, and general impact resistance. While the molecules and resins inside the coatings are important to the process, it is how powder coating is applied that gives the powder coatings their remarkable strength.
Powder Coating vs Painting
Though these two methods of applying surface coatings seem very similar, the science behind them is quite different. When painting, the pigment is carried by a wet solvent that will evaporate away and leave nothing but the pigment behind. The powder coating process works a bit differently. Powder coating is applied electrostatically to the part by use of a spray gun. The electrostatic charge that the coating receives is one of the key differences that makes a powder coat much stronger than a traditional paint finish.
One of powder coatings biggest advantages over traditional paint is that powder coating is considered a very eco-friendly finishing process. Conventional liquid paints can use harmful solvents and in some cases will emit significant amounts of Volatile Organic Compounds, or VOCs. VOCs can cause damage to the ozone and if the paint is kept indoors, can pose health risks to people exposed to them. Powder coating emits little to no VOCs and are environmentally friendly in all aspects.
The Full Powder Coating Process
It starts with just dry powder. This powder consists of polymer resins, pigments, and other additives that help with it's adhesion. By using an electrostatic gun the powder material will receive an electrical charge which attracts the powder coating to the surface of the part. The particles are forced through the electrostatic gun with small amounts of compressed air, usually ranging from 4-7 psi.
The part is electrically grounded and the coating will remain adhered to the grounded surface for as long as it retains the charge. There are recovery and retrieval systems employed to collect any excess powder. Once the part is fully coated it is placed in a curing oven, and the type of powder being used will matter once it reaches the curing stage.
There are two main types of powder coating; thermoplastic powder and thermoset powder. Thermoplastic and thermoset powders react differently in the curing oven but will still end up with the same result. Once that is chosen there is a wide variety of specific resin bases to choose from.
For more on choosing the most suitable powders for your projects, check out this article.
As the coated part reaches the optimum curing temperature within the oven, the powder particles melt and flow together to form a continuous film over the part’s surface. The cure schedule will dependent largely on the size, shape, and thickness, of the part being coated. The oven will generally be operating between 325 to 450 degrees Fahrenheit during the curing stage and will result in cure times that range anywhere from ten minutes to over an hour.
The spray method is not the only method for applying powder coating. Fluidized bed systems are a commonly used method of application as well, usually used when applying a thermoplastic coating and not a thermoset coating. When using a fluidized bed, the parts are preheated to between 400-450 degrees Fahrenheit and placed into a tank full of the powder material that has been 'fluidized' by adding in compressed air. This helps to fully coat items that are shaped irregularly such as pipe fittings and metal racks. The heat retained by the item and the length of time spent in the powder coating will determine the thickness of the coating.
Once removed from the fluidized bed, the item will be placed in another oven and heated once again, at or around the melting point of the specific powder coat used. This is to help flow out the coating and make sure the item has been coated evenly. If the heat reaches a temperature too high the coating may begin to drip or sag so it is important to keep close watch over the temperature.
Is Powder Coating Environmentally friendly?
Both powder coating media and the coating application processes emit minor amounts of VOCs and are considered non-toxic. Powder coating doesn't use any kind of toxic chemical, does not create harmful fumes, and does not contribute to air pollution. For these reasons it is highly recommended to use powder coatings on objects intended to be kept indoors. Liquid paint coatings can be a health hazardos due to the use potentially harmful solvents. Powder coating is already compliant with environmental protection standards and as long as the equipment being used is up to date with safety regulations, anyone can begin the powder coating process.
Powder coating media can also be recycled. When following the electrostatic spray process, excess coatings and over spraying is almost inevitable. Any powder materials that do not end up adhering to the surfaces being powder coated can easily be reclaimed and reused for the next suitable project. When using fluidized bed systems, there is virtually no waste at all as excess coating material will stay in the submersion tank.
To read more about all things powder coating, check out our blog.